Five factors that determine the robustness of a machine
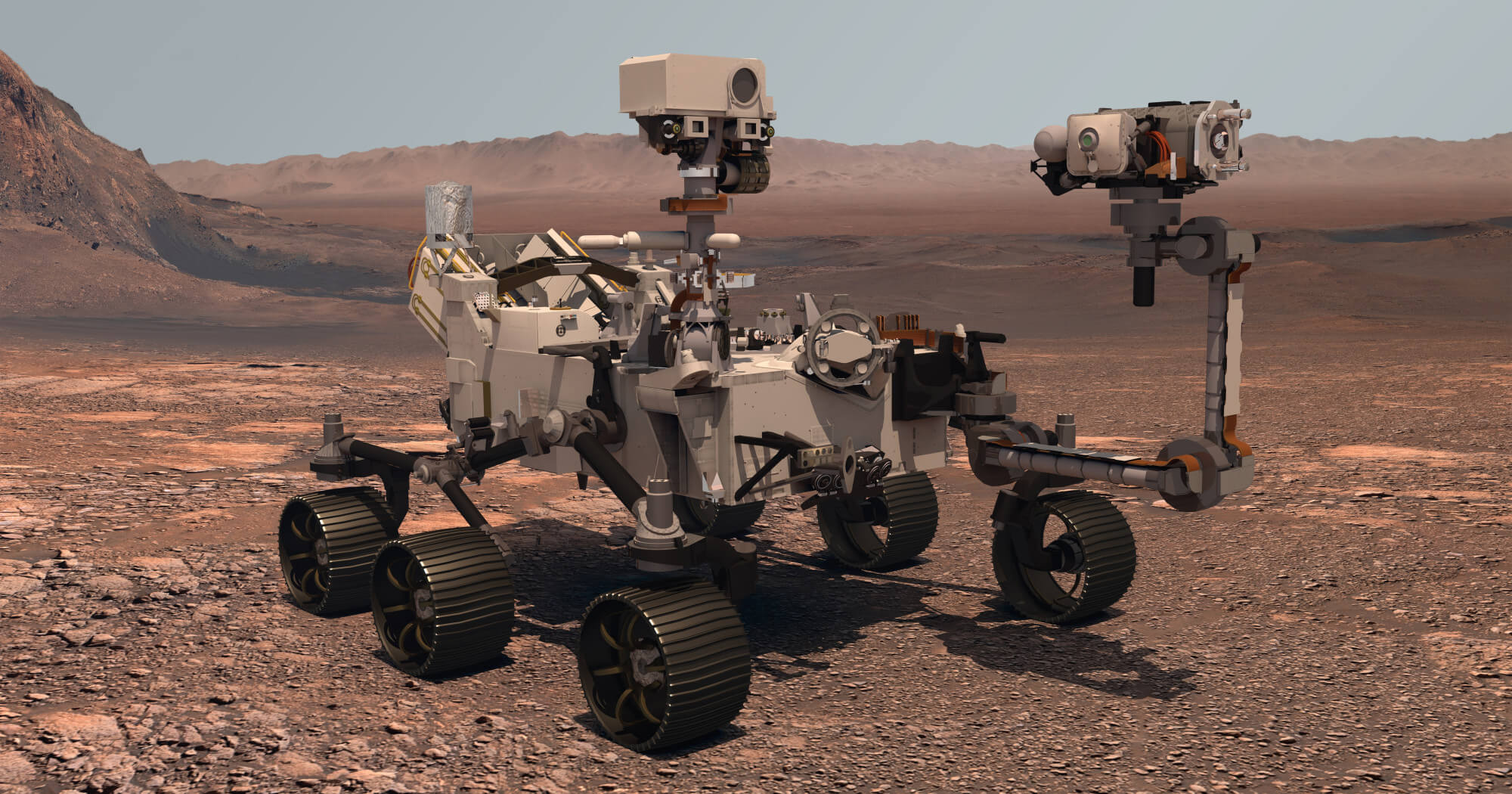
Extreme conditions
Adapting a machine to a harsh environment relies partly on the components chosen. All motors, drives, controllers, linear actuators and mechanical transmissions used must be certified, verified and tested to the highest environmental, EMC and safety standards, and therefore able to withstand extreme conditions. But what are these “extreme conditions”? A harsh environment may present itself with
the following factors, for example:
• High and low temperatures from -40°C to +70°C.
• Thermal shock, when components undergo extreme heating or cooling in a short period of time.
• Large differences in altitude within short timeframes, like an airplane taking off and quickly reaching an altitude of 12,000 metres.
• Large differences in depth within short time periods, as experienced by underwater robots that descend rapidly to depths of 7,000 metres, where pressure differences put a strain on electronic components.
• High relative humidity, up to 95% noncondensing at 25°C and up to 90% noncondensing at 42°C.
• Intense vibrations and major mechanical shocks.
This overview is far from complete. Additionally, chemical gases, fine dust, water, salt, electromagnetic interference, and radioactivity can also affect the functioning of your machine.
Five focus points
When designing a machine, it makes sense to take environmental factors into account and consider worst-case scenarios. Which extremes may be faced in a harsh environment? Once detected, the choice of material and sealing of components, for example, can be determined accordingly. Here are five factors that can be critical to the robustness of a machine:
1. Right choice of material
Substandard materials lead to failure, high repair costs and lost productivity. Do you face a risk of smearing due to liquid leaks, among other things? In this case, the use of stainless steel, for example, may be the solution. Stainless steel, hard-anodised aluminium and tough polymers are among the most common materials used to make more robust movement control components.
2. Protective coatings
In addition to the choice of material, equipment coating is also an important consideration. This particularly applies to components that require additional protection, such as those used in environments where corrosive chemicals, salt spray or immersion are involved. However, certain special coatings or greases also protect against high temperatures or exceptional vibrations, for example. The right coating can significantly increase component lifespan.
3. Dustproof and waterproof seals
Solids and liquids can not only damage a machine and lead to machine downtime, but also create dangerous situations for operators. It is therefore important that each component of a machine is sealed correctly. International protection ratings (IP code) indicate how well a component is protected against the penetration from solids and liquids. The number 6 in IP68, for example, indicates complete protection against dust. The 8 indicates that the component is watertight.
4. Impact resistance
Shock and vibration can damage materials, coatings and seals, causing malfunctions. It is therefore wise to take this into account when designing a machine, for example by adhering to standards such as IEC/EN60068-2-27 and IEC/EN600682-32. Planetary gearboxes, for example, provide better shock and vibration protection than parallel gearboxes. Consideration should also be given to avoiding rolling-element bearings.
5. Ease of maintenance
On the one hand, the moving parts of a machine wear out more quickly under difficult conditions and, on the other, frequent maintenance is not always possible due to the demanding nature of certain environments. As such, it becomes important to consider how to make machine maintenance easier, which could include opting for self-lubricating components and replacing lubricating oil with grease.
Eltrex Motion: a strong partner
We are drive specialists and, in addition to our thorough knowledge of all things motion control, we provide an extensive range of products for demanding environments, from extremely rugged single board computers, integrated I/O boards and power supplies to high strength servomotors, controllers and motors. Our project managers are usually involved in turnkey client projects from the very beginning, when Eltrex engineers work with clients to analyse environments and find the best possible solution. In addition, we not only assemble and mount individual components in our Competence Centre, but also thoroughly test and document their robustness. Working alongside our partners, we always find a solution adapted to your projects for harsh environments.
Feel free to contact us. You can reach us by phone at +31 (0)76 789 00 30 or +32 (0)3 328 07 60. You can also fill in the contact form. We will process your enquiry as soon as possible.
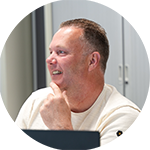