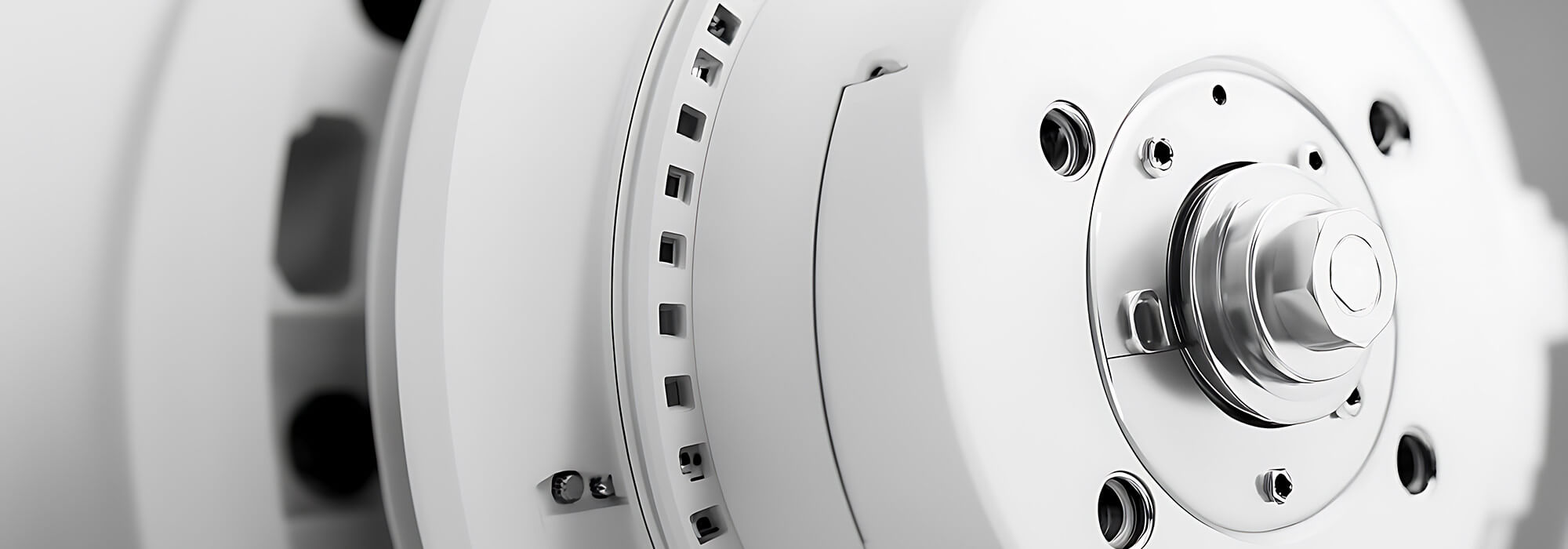
Motors
Each motor technology offers unique features and benefits. The optimal choice can significantly improve the efficiency, lifespan, and performance of your systems. Choosing the right motor requires a good understanding of the specific needs of your application and the environmental factors.
Different motor technologies
Depending on the application, the motor type must be determined. For example, in an application where the motor must constantly accelerate and decelerate, thus dynamic use, servo motors are an excellent choice. They feature high continuous torque, high peak torque, and potentially high positioning accuracy due to the necessary position sensor.
If the application is less dynamic but requires high torque, a stepper motor could be chosen. The advantage is that these motors can generate high holding torque at relatively low speeds. This may eliminate the need for a (planetary) gear box.
For applications where decentralized control and space-saving are important, such as in machines with limited space or where modularity is required, integrated motors like the Duet AD, MDX+, or HFI series could offer an ideal solution. These motors combine motor, position sensor, and control in one package. They are perfect for installations that benefit from less wiring and communication protocols such as EtherCAT, CANOpen, Profinet, or RS-485.
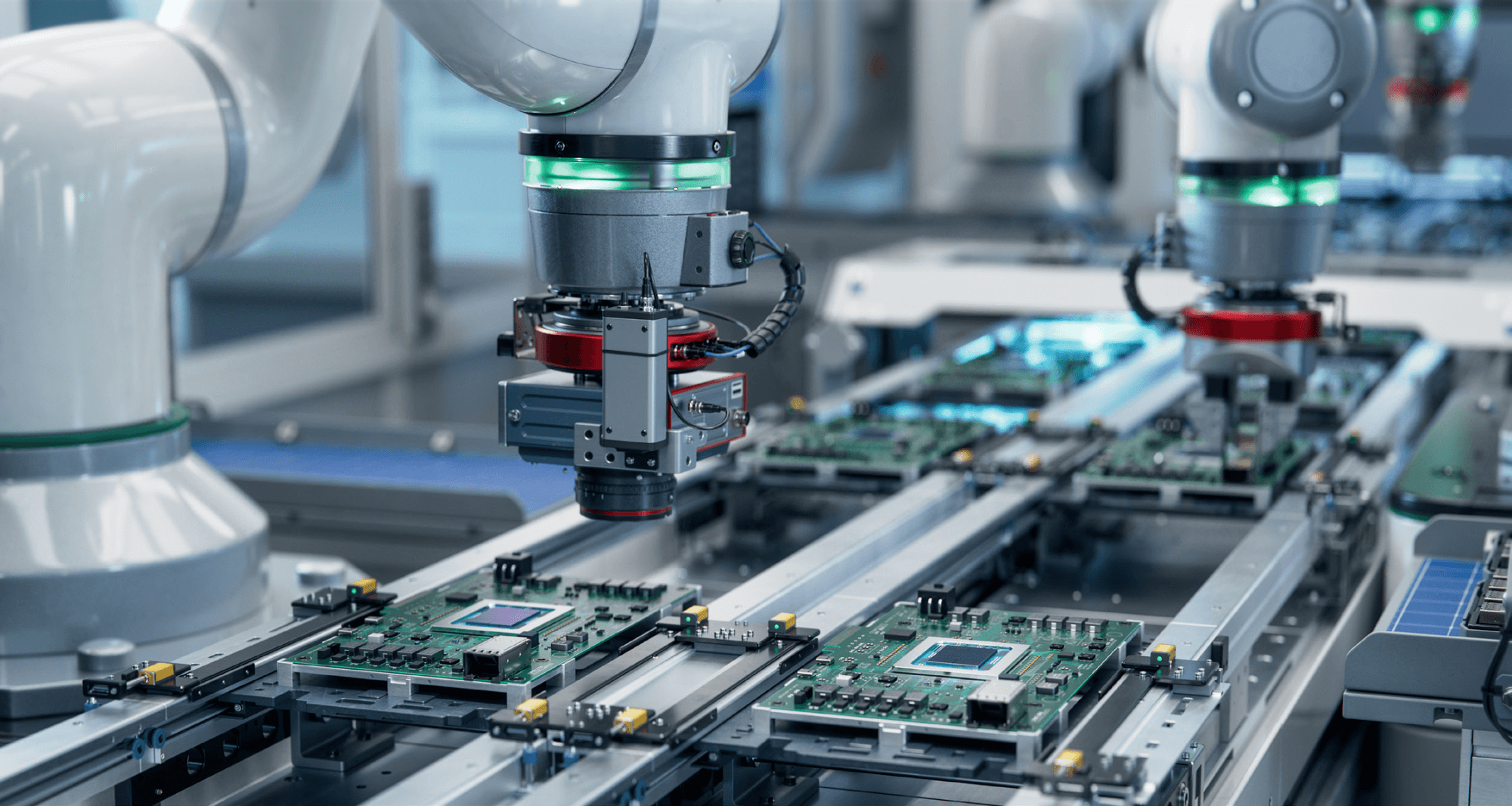
The benefits of a position sensor in the motor
In a positioning solution, stepper motors can be chosen to be controlled open-loop, i.e., without a position sensor. This is a very cost-effective option, but if the motor is not correctly dimensioned, it can stall without being detected. Brushless servo motors are often equipped with a position sensor. These can be incremental or absolute encoders or, for special applications, resolvers. Incremental encoders often provide a pulse train or analog signal, while absolute encoders often work based on a communication protocol, such as Hiperface, Endat, BiSS-C, or SSI. Encoders that are necessary for functional safety in an application are also possible.
With or without reduction
In many cases, the optimal operating range of servo motors is between 2,000 and 3,000 rpm. There are situations where a lower speed is required in the application. In such a case, the motor can be equipped with a gearbox. Often, a more compact motor can be used to reduce the speed and increase the torque. We can mount various gearbox variants on our motors, such as worm, planetary, or harmonic technologies.
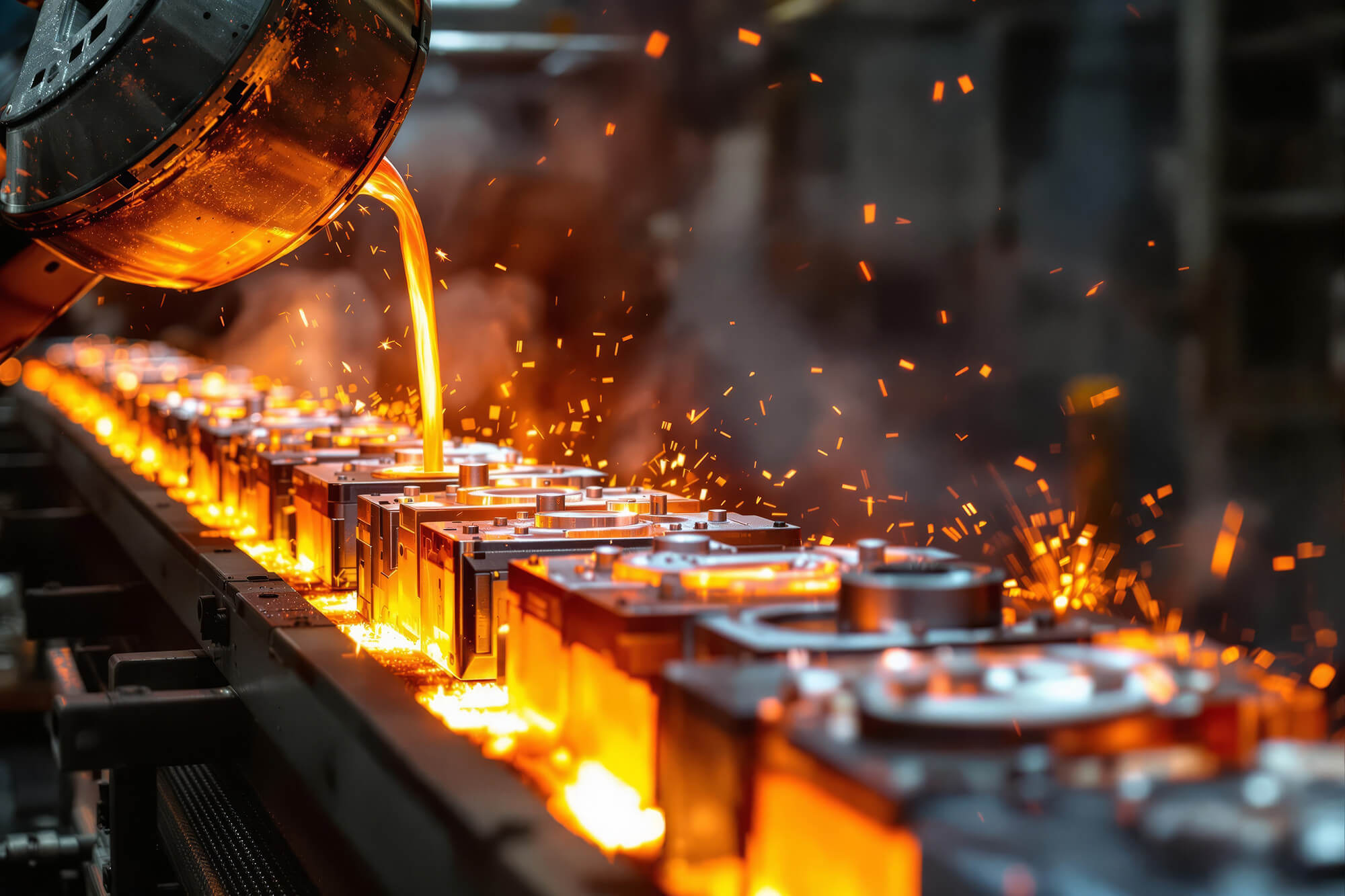
Environment in which the motor is used
Most motors are standard applicable within a temperature range of 0°C to 40°C. By using suitable materials, this temperature range can be extended both downwards and upwards. IP classification is also important, especially in applications where dust and/or water resistance is crucial.
Finally, reliability and minimal maintenance are always important, especially in applications that are used intensively or are critical for essential operations. Gearless motors, such as the MTR series, are ideal where durability and minimal maintenance are priorities, as they lack wear-sensitive parts like pinions.
For applications such as intralogistics or conveyor belts, this can significantly reduce operational downtime and maintenance costs.
Your motor, our expertise
By considering the above factors and aligning them with the strengths of Eltrex's motor portfolio, customers can find solutions that are not only effective for their current needs but also adaptable for future requirements. With technical support and expertise from our engineering team, Eltrex is ready to guide customers in choosing the best motor tailored to the specific needs of each application.
Feel free to contact us. You can reach us by phone at +31 (0)76 789 00 30 or +32 (0)3 328 07 60. You can also fill in the contact form. We will process your enquiry as soon as possible.
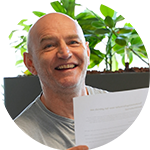