Elektromechanical versus Pneumatic & Hydraulic
No matter how simple or complex the linear motion system, at the most basic level they all have one thing in common. Moving an object or load over a linear distance. Hydraulic, pneumatic or electromechanical can be used for the drive system. How do you decide?
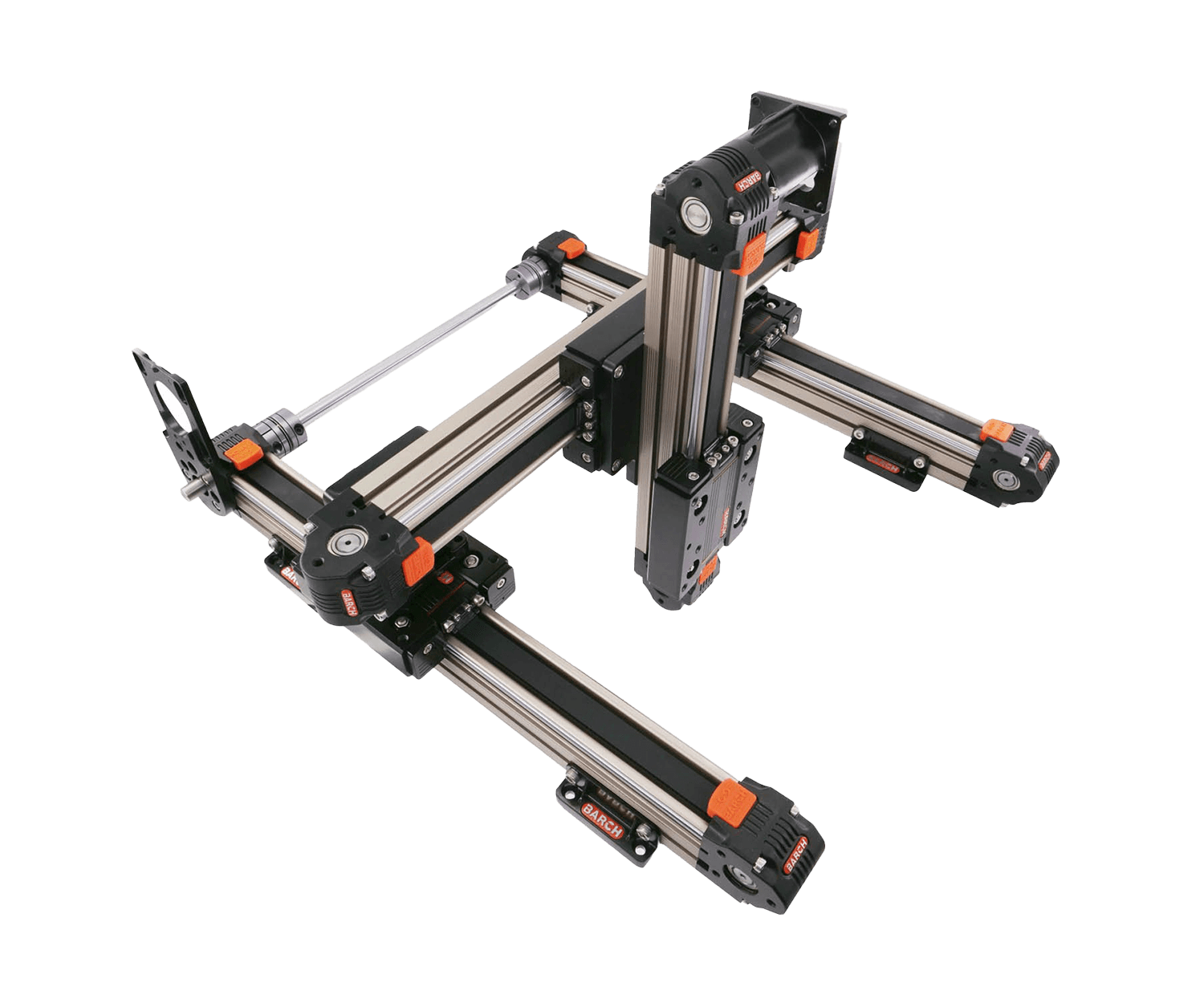
Linear Drive
Linear motion applications are found all over the place these days. They vary from relatively simple systems, such as low-cost seat actuators in passenger cars to complex multi-axle systems, complete with steering for e.g. closed-loop controls.
No matter how simple or complex the linear motion system, at the most basic level they all have one thing in common. Moving an object or load over a linear distance in a given amount of time, using a linear guide and a linear drive to control movements with different variables and complexity.
In other words, everything that has to go in a straight line is a linear movement. Eltrex answers all your questions about linear drives, both simple and complex. Our product specialists will help you quickly convert your design into the best possible solution, from design, through prototyping and testing to the final product.
Electromechanical vs Pneumatic & Hydraulic
You will find them in every industry and sector—machines and devices that operate based on linear motion or a combination of multiple linear movements. From pick-and-place systems in a canning factory to the selection mechanism in a vending machine, linear actuators are widely used. Anyone who has walked through a production hall will undoubtedly recognise pneumatic or hydraulic cylinders, which are commonly utilised. For decades, compressed air and hydraulic oil have been the standard mediums for driving linear movements in machines and applications. However, this is gradually changing. With the rise of high-tech electromechanical actuators, there is now a highly viable alternative to pneumatics and hydraulics—offering a whole range of additional benefits.
The Drawbacks of Pneumatics & Hydraulics
Using compressed air or hydraulics to drive a complex machine comes with many challenges. Every linear movement must be connected via pneumatic or hydraulic lines to an air compressor or hydraulic power unit. This requires a significant investment of resources, space, and time, while also reducing the flexibility of the installation or configuration.
Other disadvantages of pneumatic and hydraulic systems include positioning accuracy, susceptibility to wear and corrosion, and inefficiencies due to compressibility. Air and liquids are compressible to some extent and sensitive to temperature fluctuations, which negatively impacts accuracy and reliability. Furthermore, pneumatic and hydraulic pipes and cylinders are prone to wear and corrosion, and they are not always suitable for higher IP protection classes.
All of these factors result in additional work for installers and maintenance engineers, leading to higher costs, longer downtimes, and reduced flexibility. On top of that, energy consumption is high—pneumatic or hydraulic systems must always be in operation to exert force, which adds to inefficiency.
The Advantages of Electromechanical Actuators
Replacing all pneumatic and hydraulic actuators in an average system with electromechanical linear actuators reveals an immediate difference. The complex network of air and fluid pipes disappears, replaced by simple electrical cabling. Moreover, this cabling does not require bulky conduits to connect to a distant compressor or power unit. A nearby power source is sufficient, and thanks to modern intelligent bus technology, a network or Wi-Fi connection to the control room is enough to maintain complete control over the application.
With electromechanical actuators, issues related to compression are eliminated entirely, ensuring greater precision. Corrosion from air or fluid is no longer a concern, and energy consumption is significantly lower since an electric drive only uses power when movement is required.
Pros and Cons at a Glance
|
Advantages |
Disadvantages |
Hydraulic |
|
|
Pneumatic |
|
|
Elektromechanical |
|
|
Feel free to contact us. You can reach us by phone at +31 (0)76 789 00 30 or +32 (0)3 328 07 60. You can also fill in the contact form. We will process your enquiry as soon as possible.
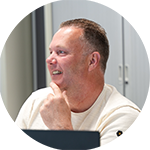